Open here for our page navigation
Aluminum Fluoride Granules
AlF3, 99.999% pure, 1 - 4 mm
Overview:
Aluminum Fluoride (AlF₃) is a high-purity material widely used in thin-film production, optics, and advanced coatings. It is characterized by its low refractive index, making it particularly effective for coatings in the UV, visible (VIS), and infrared (IR) spectral ranges. In granular form, AlF₃ is especially suited for Physical Vapor Deposition (PVD) processes.
Key Properties:
- Excellent thermal stability – withstands high temperatures without degradation.
- Low refractive index – ideal for anti-reflective coatings.
- Strong chemical resistance – highly durable in various environmental conditions.
Applications:
- Thin-Film Deposition – Essential for PVD processes, enabling the creation of thin films and coatings used in optical, electronic, and protective applications.
- Optical Coatings – Used in anti-reflective (AR) coatings, enhancing the efficiency of lenses, mirrors, and optical systems by minimizing reflection and improving clarity.
- Metallurgical Flux – Serves as a flux in aluminum smelting, facilitating impurity removal and increasing process efficiency.
- AR and HR coatings for laser optics in the VUV and DUV (e.g. at excimer wavelengths 157 nm, 193 nm, 222 nm …)
THIN FILM PROPERTIES:
Range of transparency 150 nm – 10 µm
Refractive index at
• 220 nm ~ 1.39 – 1.41
• 550 nm ~ 1.36
• 3 µm ~ 1.28 – 1.30
Absorption edge ~ 150 nm
Thin film stress Tensile (low)
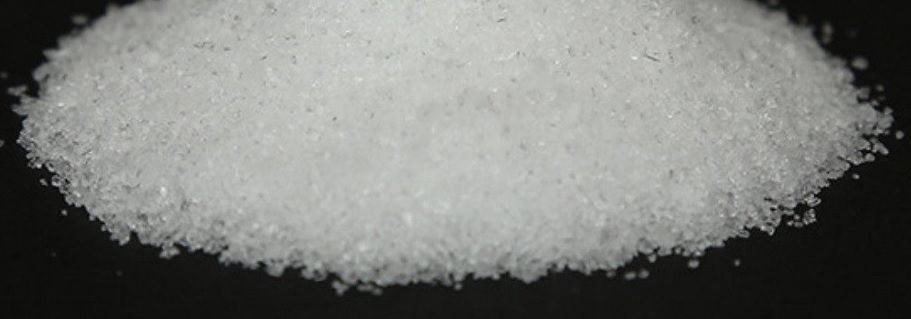
NOTES FOR EVAPORATION:
Evaporator source: Preferred: resistance heater thermal evaporation Electron beam Evaporator
Liner / boat: Mo or Ta boat Copper crucible
Evaporation temperature: 800 - 1000°C
Deposition rate: 1.0 - 2.0 nm/s
Substrate temperature: 30 - 350°C, pref. 250 - 350°C
QCR-settings: Density 2.88 g/cm³, z-ratio 1.0
AlF3 thin films show an amorphous structure. They exhibit reduced thin film stress and lower surface roughness compared to MgF2.
E-beam evaporation of AlF3 is possible, but usually avoided, due to the tendency of AlF3 to show stronger spitting compared to MgF2 and the other UV fluorides. Evaporation from a baffled box is recommended to achieve low defect densities. A substrate temperature in the range of 250 to 350°C is required for dense film structures.